LEAN 6 QMS
Consulting Services
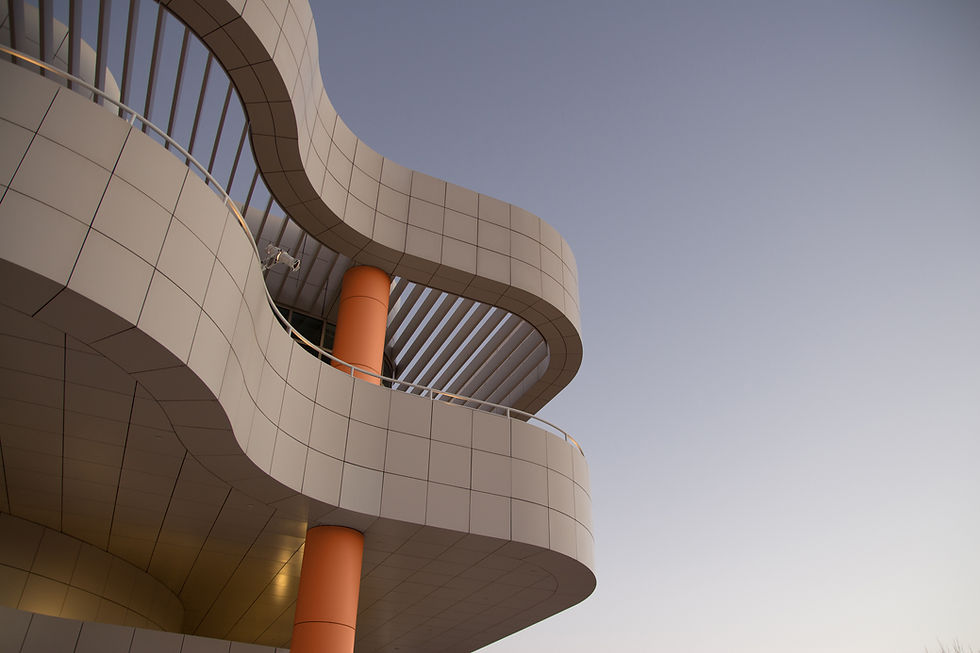
🔍The Power of the 5 Why’s in Root Cause Analysis🔍
Nov 16, 2024
1 min read
0
0
0

In any manufacturing or quality control process, issues arise. The key to effective problem-solving isn’t just addressing the surface symptom but identifying the root cause. This is where the 5 Why’s methodology comes in a simple yet powerful approach to get to the core of any issue.
By asking “Why?” repeatedly (typically five times), we dig deeper with each answer, uncovering underlying causes that may not be obvious at first glance. This process not only helps in identifying the root cause but also enables sustainable corrective actions, reducing future fallout and improving product quality.
The 5 Why’s methodology is essential for:
✅ Maintaining operational efficiency
✅ Boosting product quality
✅ Strengthening process reliability
Whether it’s a design flaw, a procedural gap, or a material defect, identifying the root cause allows teams to prevent recurrence, optimize production throughput, and safeguard margins.
💡Have you used the 5 Why’s approach in your work? What benefits - or challenges -have you experienced with this process? Share your insights!
#RootCauseAnalysis #5Whys #LeanManufacturing #QualityManagement #ContinuousImprovement #ManufacturingExcellence #ProblemSolving #OperationalEfficiency #Lean6QMS