LEAN 6 QMS
Consulting Services
LEAN Manufacturing
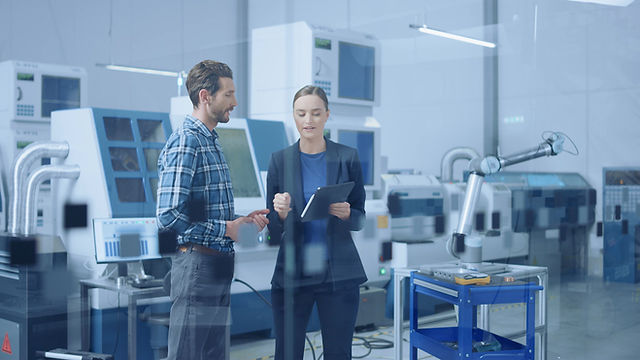
What is LEAN Manufacturing?
​
LEAN Manufacturing is a production methodology that focuses on minimizing waste within manufacturing systems while simultaneously maximizing productivity. It is derived from the Toyota Production System (TPS) and is known for its emphasis on improving efficiency, reducing costs, and delivering value to customers.
​
The core principles of LEAN Manufacturing include:
​
-
Value Identification: Defining what is valuable from the customer’s perspective. Everything that does not add value is considered waste.
​
-
Value Stream Mapping: Analyzing the entire production process, from raw materials to the finished product, to identify and eliminate steps that do not add value.
​
-
Flow: Ensuring that the production process flows smoothly without interruptions or delays. This requires eliminating bottlenecks, ensuring equipment reliability, and simplifying workflows.
​
-
Pull System: Using a pull-based system, meaning products are only manufactured in response to customer demand, rather than being pushed through the system based on forecasts.
​
-
Continuous Improvement (Kaizen): Encouraging small, incremental improvements regularly and continuously involving employees at all levels to contribute ideas for enhancing processes.
​
-
Waste Reduction (Muda): Identifying and eliminating the 7 wastes (Muda) in production, which are:
​
-
Overproduction: Producing more than what is needed.
​
-
Waiting: Idle time during production due to delays.
​
-
Transportation: Excessive movement of materials.
​
-
Overprocessing: Doing more work than necessary.
​
-
Inventory: Holding more stock than required.
​
-
Motion: Unnecessary movement of workers.
​
-
Defects: Producing defective products that require rework.
​
​
Lean manufacturing aims to streamline processes, improve quality, and reduce costs by aligning production more closely with demand, thus providing higher value to customers while using fewer resources.
​
The first step towards LEAN Manufacturing is 5S, which is considered one of the foundational steps in implementing LEAN Manufacturing. It creates the groundwork for efficiency and productivity by organizing the workplace in a structured and disciplined way. Many organizations begin their Lean journey with 5S because it establishes the fundamental discipline needed to support further Lean initiatives, such as waste reduction and continuous improvement.
​
The 5S components are:
​
-
Sort (Seiri): Eliminate unnecessary items from the workspace, keeping only what is needed.
-
Set in Order (Seiton): Arrange necessary items so that they are easy to access and return to their proper places.
-
Shine (Seiso): Clean the workspace to ensure it remains organized and that any abnormalities (such as leaks or defects) can be easily identified.
-
Standardize (Seiketsu): Establish standardized procedures for maintaining the first three steps to ensure consistency and efficiency.
-
Sustain (Shitsuke): Foster discipline and commitment to maintaining the standards set by 5S through training, communication, and regular audits.
​
By starting with 5S, organizations can establish a culture of order, cleanliness, and efficiency, which are essential for sustaining further LEAN practices like flow, pull systems, and continuous improvement (Kaizen). So, while 5S may not be the "only" first step, it is frequently used as the starting point in LEAN implementation.
​
Streamline your operations with our expert guidance. We provide tailored consulting services to optimize your manufacturing processes. Our team offers LEAN-focused training and process improvement strategies to enhance your overall productivity and effectiveness.​
Lean Solutions
Optimize your operations with our Lean 6 Sigma expertise. We help you identify inefficiencies, reduce waste, and enhance productivity. We will work closely with your team to implement sustainable Lean practices for long-term success.
Quality Management
Enhance your quality standards with our QMS consulting services. We assist in developing robust quality processes, conducting internal audits, and preparing for external certifications. Let us guide you towards excellence in quality management.
Certification Prep
Prepare for certification with our comprehensive support. We offer mock audits, corrective action assistance, and documentation review to ensure your readiness. We are here to help you achieve your certification goals.